
Sovereign Logistics Handle Cement Plant Project Shipment
26th August 2015
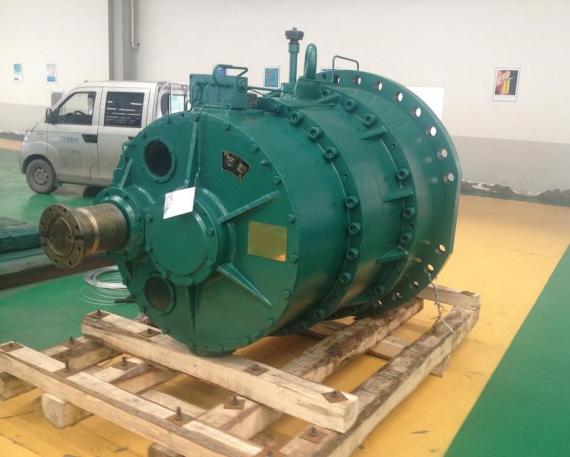
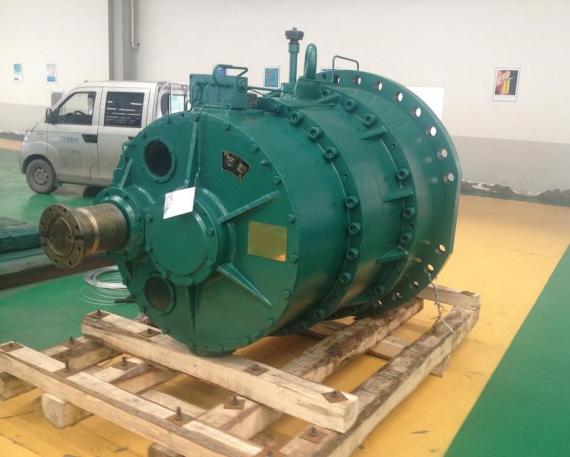
PCN members in Kenya, Sovereign Logistics Limited are part of the Express Shipping & Logistics (EA) Group. The company are pleased to report a recent project photographed and outlined below.
Client
The client's business involves the manufacturing of cement and other cement-based products. The company was started in 2013 and Sovereign Logistics offered full logistics services to import, clear and deliver the entire cement plant, including the mill. This is where we built the confidence.
Using our chartering, ships agency and logistics services, we have continued to serve their bulk clinker ships - the raw material used in cement manufacturing. In 2013, we handled 1,050,000.5mts, in 2014: 1,133,996.82mts and so far in 2015: 1,254,314mts. We have also handled all their spares imports. This business model is replicated for many of our customers in Kenya, Uganda, Tanzania, Rwanda and Burundi. Our market share in the region is around 90%.
Riding on the distinctive services of Sovereign Logistics, our client performed very well and attained a market share of 30% within two years of operations. However, as fate would be, the company did not take contingency plans to cater for the failure of essential parts such as the gearbox.
Project Details
The problem arose when the cement mill gearbox, a very important component of the plant, broke down. The company's appointed engineers were contracted to complete the repair within the shortest time possible. However, this proved difficult as even removing the mammoth 14tn machine from the kiln was not an easy task and there was no guarantee that the gearbox would be repairable. Therefore, our client decided to import a new one from China.
Import
We received a distress call from our client as no production was possible and we worked out the best options to bring the gear box to its new home. The first option was to ship in a 20’ open top container. However, the transit time from Guangzhou to Mombasa port was 30+ days and this was not acceptable as the company was losing USD $50,000 per day in actual and opportunity costs.
Airfreight
The only option was to move the large machine as airfreight. We approached several airlines with the capacity and capability to handle the shipment and only one accepted - Saudi Arabia Airlines. Just as we breathed a sigh of relief, a new challenge surfaced - The airline only calls at Guangzhou airport once a week and the distance from the manufacturer to meet the flight was 2,000 miles.
Packaging
Another challenge was the packaging which took 2 days as heavy wood was required to hold the base of the crate, while minimizing the cargo's gross weight. In addition, high tensile wires were used to lash the gearbox tightly so there was no possibility of movement during transit.
After confirmation by the packaging expert, the crate was lifted to a low-loader. This was also a challenge because the safe working load (SWL) was over 14tns.
Road Haulage
The 2,000 miles to the airport ran smoothly as the driver knew the urgency of the shipment. The cargo was treated as if it were perishable.
The shipment made it to GGZ airport within two days. However, the worst happened as it missed that week’s flight by only 2 hours. Now, our partners and the SV staff worked quickly and smartly to utilise all available options. At this point, the freight payable was not a factor as the client was even willing to charter a plane at USD $250,000.
Routing
The original SV route was Guangzhou-Jeddah-Nairobi. However, the ingenuity of the SV route planner resulted in a new routing of Guangzhou-Oman-Jeddah-Nairobi, because the Oman flight called at Guangzhou twice a week. However, it was then realised that the connection flight from Guangzhou to Oman was smaller and could not accommodate the large cargo. Therefore, we were forced to return to the initial route as it was the only option. The cargo stayed at the warehouse in Guangzhou for one week until the next flight was pre-alerted when the next challenge began.
Stowage
The 14tn gearbox proved a difficult task for the stowage clerks. The plane had to be stowed in the middle haul to maintain the balance and it was imperative that the shipment did not move or tilt. SV had to call in a special stowage engineer who used all their knowledge to correctly stow the cargo.
The shipment left Guangzhou and the destination team kept vigil at the SV offices for updates. In Jeddah, the same issue of stowage occurred which resulted in the shipment having to wait for another week.
Destination
Once the cargo was airborne on its final journey, our operations team used our very good working relationship with the customs and airport authorities in Nairobi to arrange for an advance cargo release. This was made easier using our A.E.O. and ISO status and as the flight arrived at 2100hrs we were able to clear the shipment at night against the usual custom operations of the airport due to its urgent nature.
On Site
There was no time to waste and the truck and crane were on standby once the plane had touched down. Having completed the prior clearance, the shipment was quickly towed in rollers to the side of the truck. The crane winched it to the truck and the weight was felt immediately by the shocks of the truck.
The truck had no problems driving to the site where the engineers worked overnight and by the morning, the kiln was grinding cement again. Although it took more than twenty days for the gearbox to reach its destination, many challenges were overcome and the client were pleased with our expertise and the dedication in which we handled the operation.
Downloads
Name | Action |
---|---|
Full Project Details | download |
